
If your organisation’s documentation doesn’t meet this standard it will result in regulatory non-compliance, significant costs to your organisation in terms of resources to rectify issues, and may impact your organisation’s reputation for example as a result of delays in processing customer orders or failing to deliver a quality product or service to your customer.
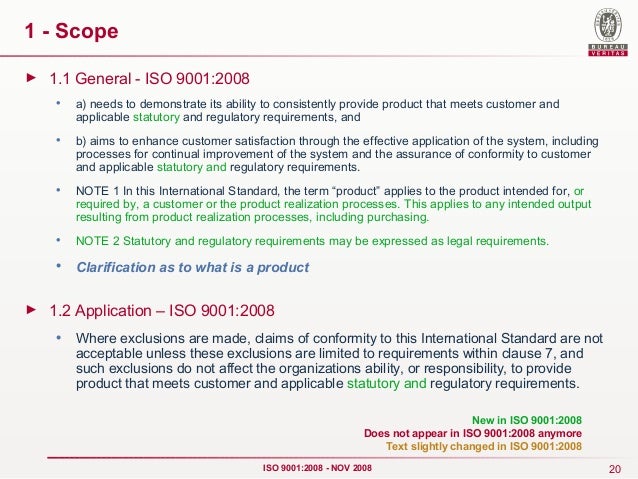

Is your QMS documentation fit for purpose?įit for purpose QMS documentation ensures that all processes are understood and consistently executed by employees such that a quality product/service is delivered to the customer each and every time.

It is evident that good documentation is critical to a functioning QMS, in fact it forms the foundation of the organisation’s QMS as it gives effect to the QMS for the life-cycle of the product/service being delivered. Documentation is also required for regulatory purposes and must demonstrate the effective planning, operation and control of the organisation’s processes and the implementation and continual improvement of the effectiveness of its QMS. Documentation must also be lean, as too many documents will result in the processes and respective QMS being harder to both use and maintain while also being bureaucratic. QMS documentation fulfills many functions such as communication of information, providing evidence of conformity and sharing knowledge and as such many different types and levels of documents are needed, for example a quality manual, quality policy, documented procedures and work instructions.Ī one size fits all approach won’t work, each document type must be fit for purpose such that it is readily understood by relevant personnel and can be effectively implemented.

The QMS documentation must accurately and succinctly document the organisation’s structure, procedures, processes and resources.Ī well designed documented system has many benefits, it ensures quality standards are routinely met, minimizes the potential for error, reduces downtime when deviations occur due to being able to quickly access relevant data, and allows for easy monitoring of the processes such that process outputs are analysed and appropriate adjustments are made. A QMS helps to coordinate and direct an organization’s activities to meet customer and regulatory requirements and continually improve its effectiveness and efficiency. A quality management system (QMS) is a formalized system that documents processes, procedures, and responsibilities for achieving quality policies and objectives and thus consistently delivering a quality product or service to the customer.
